Meet Sensemore: The system that monitors factory machine health
Sensomore’s plant monitoring systems are just the ticket for reducing machine downtime.
Modern factories tend to come packed with large amounts of expensive and complex machinery within their production lines. For maximum efficiency, this equipment needs to run near constantly without any issues or delays.
But, machines can and do break over time as parts become worn and need to be replaced. For most machines, being physical things, this is an inevitability and something that can’t really be avoided.
While some machines are less complex than others, there is usually a time when a part will need to the swapped out at some point. This process not only effectively puts the machine out of operation while the repairs are completed, but also impacts the production line of the factory.
For this reason, many factories have advanced maintenance programs in place to monitor and check their machines for problems to help reduce the downtime of their plant. However, all too often, this requires specialists engineers or other staff members to operate and maintain an effective planned maintenance program that is entirely dependent on the competence and diligence of those staff members.
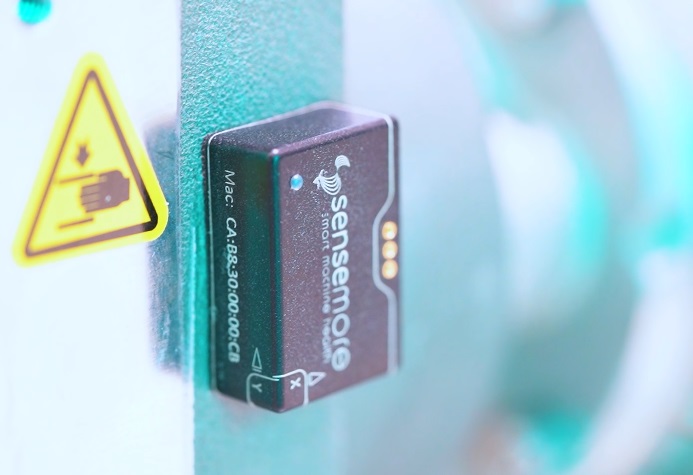
When critical elements in the fabrication line are out of action, it can cost the factory tens of thousands, even millions, of dollars every second, minute, or hour. It can also impact other elements of the factory production line if a part critically and unexpectantly fails, further compounding the problem.
Like anything in life, it would be much easier and more efficient to have some form of an automated monitoring system to identify which machines, and parts, are close to or require immediate replacement or repair.
This is where systems like those developed by a company called Sensemore come into their own. They provide a one-stop-shop solution of hardware and software to offer a market-leading solution to help factory owners decrease their machine downtime and maximize the efficiency of their plant.
Sensemore’s suite of specialists sensors comes in a range of sizes and applications and can be fitted to critical parts on the factory production line to provide 24 hours, 7 days a week monitoring of machines without the need for constant human interaction.
Guided by their motto of “Smart Machine Health”, their machine monitoring systems are second-to-none.
Any installed sensors relay their data Sensemore’s own developed AI-powered software is able to generate reports and other data on the current status of a particular part. It can also provide early warnings about which parts, if any, will need urgent attention in the immediate or near future.
Access to this kind of information is worth its weight in gold and can severely reduce downtime of machines in the production line. In fact, by as much as 30%, and reduce costs of replacement parts by somewhere in the order of 20%.
Their sensors are some of the best on the market, and, interestingly enough, one of them is the smallest of its kind. This means that the sensors can be fitted to most parts of the machine without unduly impacting their regular day-to-day operation.
These little smart sensors can be attached to pretty much any part of a machine from motors, to actuators, to any other part that needs to be monitored.
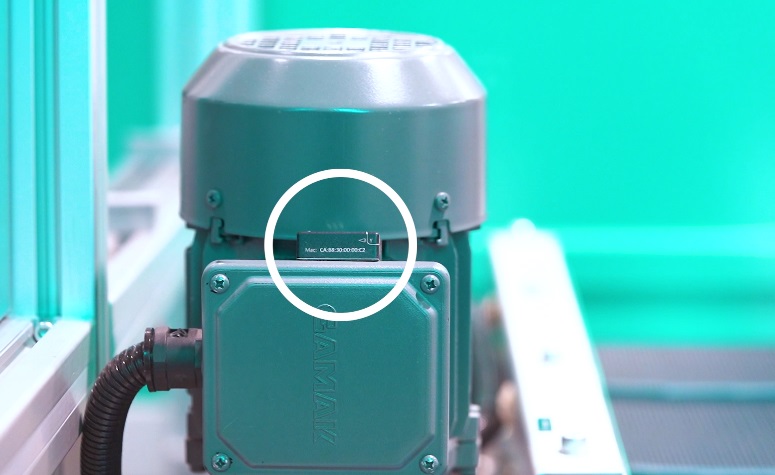
The core of the system is its integrated approach to sophisticated hardware sensors at the “business end”, and its sophisticated AI software “back end”. This combination is able to detect common faults with machines like oil whirl, mechanical losses, cavitation, or cracked gears, to name but a few.
Sensors can be wired or wireless and, depending on the particular sensor, can be readily mounted to most metal machines. Their “Infinity” model, for example, comes with a small magnet to allow it to be placed with ease on a particular machine.
Wired sensors are ideal for those situations where wireless communications or the presence of batteries is not a viable option.
It also comes with Bluetooth, enabling it to be controlled using portable digital devices like a smartphone – once the proprietary application has been installed of course.
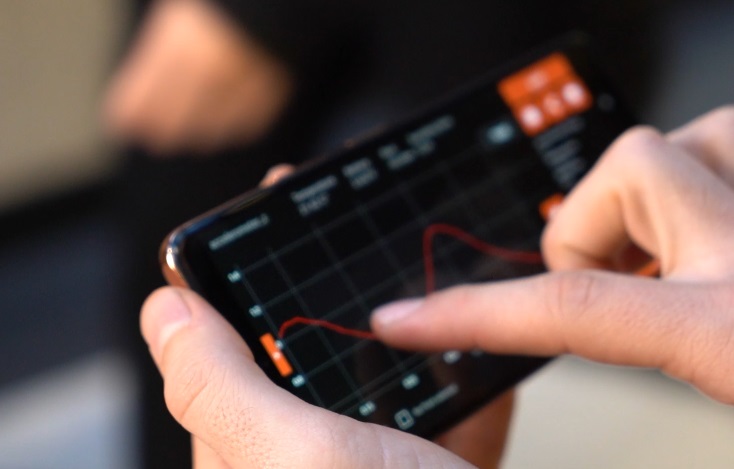
Another amazing feature of the Sensemore solution is its open-source API. This enables customers the potential to develop their own software solutions to gather and analyze data as they see fit.
With solutions like that developed by Sensemore, factory owners can rest assured that their production lines are in good hands.